

Six sigma is also the name of a set of techniques and tools for process improvement introduced by engineer Bill Smith while working at Motorola and later made famous by General Electric claiming to save up to 1 trillion dollars by using Six-Sigma under Jack Welch in the final decade of the 20-th century. A minimum standard for industrial production is three sigma. However, not all processes are designed with this level of quality assurance. The above can be visualized by comparing the specifications to the process variability as shown on the six-sigma chart below.Īs you can see, the probability that a process having control at the six sigma level will result in defects is miniscule, even with a large amount of produce. A process which produces more defects per million opportunities (has higher DMPO) will have a lower sigma level, signifying that it results either in more waste, if defects are captured before they reach the consumer, or in more poorly serviced customers, making it more expensive to produce a given number of outputs which are up to specification. A process controlled at a level of six sigma (6σ) is a process whose variability is controlled in such a manner that it produces an out-of-specification output (defect) twice in 1 billion opportunities. Why do we need to measure sigma in the first place? All processes exhibit variability over time and all measurements taken on samples of the process output are subject to additional variability simply due to the fact of sampling. A process sigma calculator is applicable in all of these scenarios, and more. A service desk may monitor performance of servicing customers by checking the length of interactions, the number of interactions required to resolve an issue, and customer feedback. For example, a production line for steel sheets coated with Polyvinyl chloride may control the width, length, and thickness of the sheets, as well as the thickness, color, and uniformity of the PVC coating. A process is usually controlled for several specifications. In industrial control of production quality and in project management in general where a process of any kind needs to be controlled for quality, the quality is assured by taking measurements on samples from the output of the process and comparing them to a specification.
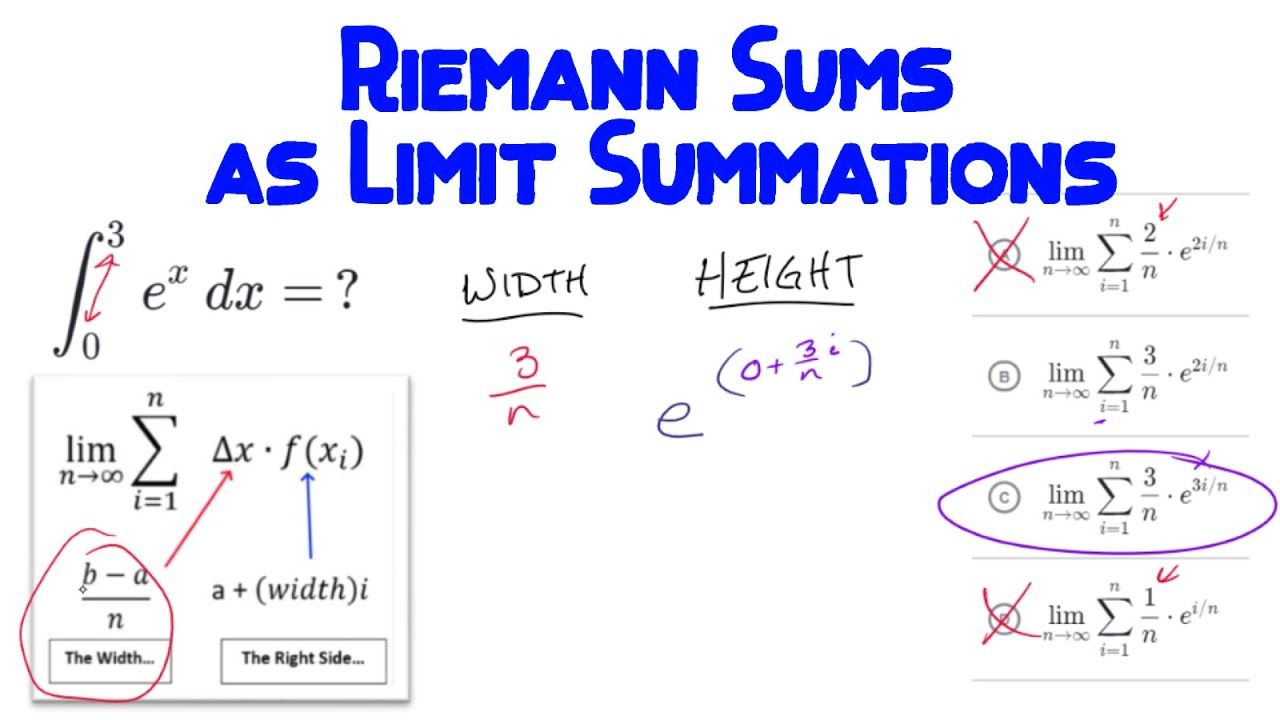
LIMIT SIGMA NOTATION CALCULATOR FULL
Entering defects, number of units and number of opportunities per unit (the number of specifications that need to be controlled for quality for each unit, defect opportunities per unit) results in the full output of the calculator, including DPM, percentage of defect units, and rolled throughput yield on top of the outputs covered so far. Entering the number of defects and total opportunities for a defect to occur outputs the control level (sigma), yield, percent defects and DPMO. The minimum required input is DPMO in which case the six sigma calculator (not to be confused with a sigma notation calculator!) outputs the corresponding sigma level, standard yield and percent defects. percentage of defect units from the total production.
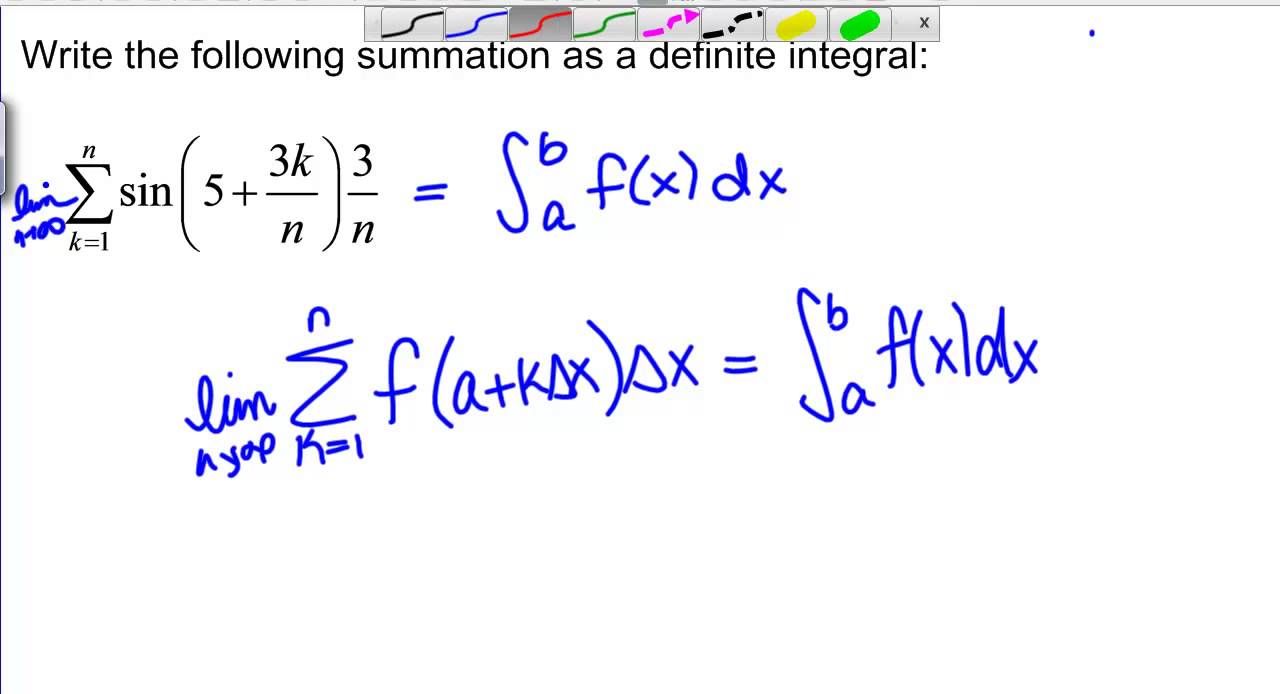
defects per million opportunities (DPMO, a.k.a.percentage of defects from total opportunities of the process to produce a defect.yield in terms of acceptable products or services delivered (rolled throughput yield, RTY).yield in terms of opportunities which did not result in a defect (standard yield).sigma level of the process (shows how well it is controlled relative to acceptance standard).Depending on the input, the output consists of: This sigma calculator can be used to estimate the sigma level of a process (of producing units or delivering a service) based on the ratio of defects it results in.
